Manufacturing in a pandemic
Staying productive while staying safe
Manufacturing is a hands-on business. How do you produce tangible products during a pandemic? We sat down with David Wright, VP of Operations at Elements, to talk about how Elements has made it work.
Q: This pandemic has been hard on so many businesses. How is it impacting Elements?
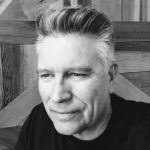
David Wright, VP of Operations, Elements Manufacturing
Wright: When people stopped going to office buildings in March of 2020, many commercial office remodels were put on hold or went away altogether. We were fortunate to have a diverse set of projects going, including senior housing and others that were large and, in some cases, deemed essential. In July things got quiet in a way we have never seen before so we moved quickly to increase our residential sales. An exciting part of this was development of Silicon Valley Cabinets, a new brand that allows homeowners and residential contractors to design their own cabinets in a browser. Increasing residential work feels like getting back to our roots. We’ve also been doing a bang-up business in panel processing for closet companies, a very hot market right now.
Q: Can you share any specifics about changes you have made?
Wright: Adding Covid safety to our processes has definitely added complexity. We have always been a very safety-minded company with a sharp focus on the well-being of our team, but Covid forced us to go further. Here’s a quick list of actions that allowed us to keep operating while keeping our workers, customers and partners safe:
- Material handling, cutting, machining and assembling – we’re fortunate to have a large shop. Step one was to spread everyone out as much as possible, require masks at all times and get serious about distancing. Step two was how to work by yourself. We also open all doors, including large roll-ups. It makes the shop unpleasantly cold but the ventilation makes it seem like being outside.
- Installing – Job sites have become very strict on taking temperatures, contact tracing and covid safety communication. General contractors have gotten very good at keeping their job sites safe and communicating with us when someone tests positive.
- Meetings – they mostly happen outside or in the shop with people spread way out to social distance. For office folks of course it’s a lot of Zoom. We have also limited the number of people that can be in a room to 3 at a time.
- Office staff – most of our office team, including our drafting people, are now working from home.
- Cleaning – we wipe down surfaces constantly. We even paid a team of professionals to come in and fog the entire facility. Holly in our office deserves a special medal for her diligence in keeping door knobs, handles, etc. clean.
- Temperature checks – Twice each day everyone takes their temperature and answers a few questions to confirm no one has a fever.
- Masks. We all wear them all day and require anyone that enters the building wear them as well. The hassle with the masks is that they make your protective lenses fog up. Protective lenses are required PPE in our shop.
- Training – everyone is tired of talking about it but we do it anyway; we do near-constant reminders and news updates as we learn new information about staying safe and abiding by State and County Covid rules.
- Travel advisories, testing and quarantines. Anyone can go anywhere, of course, but our staff knows that if they travel outside the area we will ask that they self-quarantine or get tested. Many of us have had to self-quarantine after interacting with people we thought might be covid-positive.
Q: You mentioned changes to technology. What has changed?
Wright: The first thing we did was the same as everyone else: VPN + Remote Desktop to allow our office staff to access our network from their homes. The second change is more custom. About two years ago we took on an ambitious project: to build a new interface to our SQL-based ERP system using FileMaker Pro. The new interface can read and write to the ERP database in a fast, flexible, user-friendly and searchable way. It also makes custom reports much easier. We call it FMPSI (FileMaker Pro System Integration), and it has sped up our ability to estimate jobs and allows us to access this information from anywhere via the web interface to the product. We had no idea the pandemic was coming, of course – we just got lucky putting this new technology in place when we did.
Q: How can residential customers interact with you safely?
Wright: Glad you asked! We just recently turned on a tool that allows a homeowner to design their own cabinets, for free in a browser, from the comfort of their own home. It gives them control over their design and helps us reduce design and drafting costs. You can try at www.siliconvalleycabinets.com. Silicon Valley Cabinets is a division of Elements.